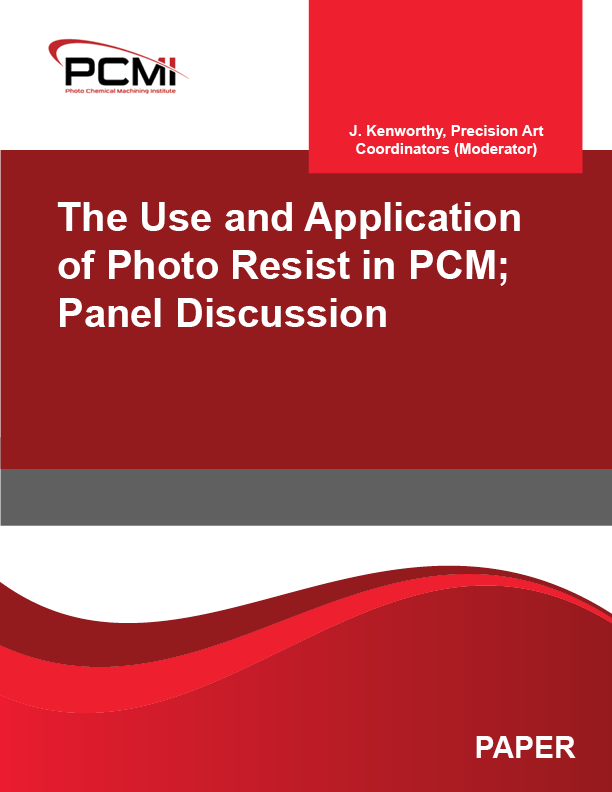
The Development of an Aqueous-Working Etch Resist for the PCM Market – Synergy or Symbiosis?
Dip coating of liquid resists for Photochemical Machining (PCM) is a well known and understood process, and has ‘been around’ probably since the industry started. The original etch resists were very simple formulations, but were well suited to the process requirements of their day. Bringing this process up to date, there are now greater environmental, cost and process requirements on PCM resists than ever before. The development, therefore, of a new photoimageable etch resist for PCM must be able to move with these changing requirements. Traditional product development consists of three distinct stages:
- The initial research and development phase in the laboratory, which can be long winded and go through many changes of direction.
- The fledgling product can then be beta tested at an end user’s facility, to gain experience and provide ‘real’ user information, rather than laboratory values.
- Full commercialization of the product.
This total process can take some time, and there is always a possibility that the product developed no longer meets the customer requirements when it comes to beta- testing. One way to shorten this procedure is to work closely together with an end-user from the start, thus developing a product that is uniquely tailored for a specific market. This procedure could therefore be defined as a symbiotic process between the two companies. The following report gives an example of such a process, and details the collaboration between a resist supplier (Coates) and consumer (Photofabrication), to develop an etch resist for the Photochemical Machining market. In doing so, it is hoped that the value of such a partnership is demonstrated.
$60.00