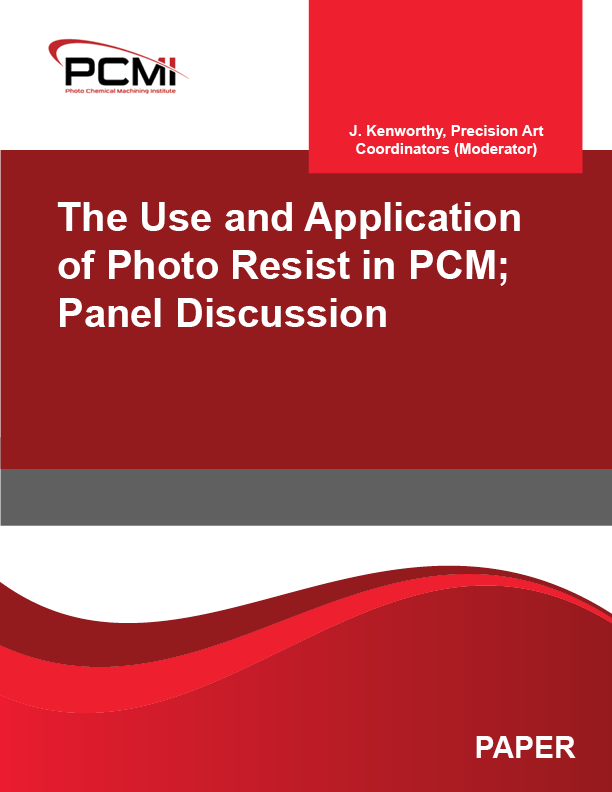
Nickel Extraction from Ferric Chloride Etchant
The case for the extraction of nickel from spent ferric chloride etchant was put forward in an earlier paper. Nickel is a useful alloying agent for its corrosion resistance & strength properties (especially at high temperatures) and for its ductility and magnetic properties. Typical applications involving etched nickel-alloy components include; semi-conductor lead frames, cathode ray tube shadow masks, filters, meshes, and springs.
However, nickel affects the etching process detrimentally, resulting in a slower etch rate and rougher surface finish. Typically, once the concentration of the dissolved nickel has reached a certain threshold level – the surface finish of the etched component is often no longer acceptable.
For reasons stated in the previous paper, it is desirable to regenerate the etchant. Nickel byproducts resulting from the etching process will not hinder the etchant regeneration process, but the “regenerated” etchant will still be contaminated. The manufacturer has two choices. They are either to replace the etchant and accept the associated costs of proper deposal of the spent etchant (ie. compliance with legislation), replacement and downtime costs or to regenerate the etchant but also remove the nickel byproduct. Costs are associated with the etchant regeneration and nickel recovery processes.
A model was put forward which indicated costs for the regeneration of ferric chloride based on varying production levels in the etching of nickel and nickel-alloy products. The completion of the model would involve the inclusion of the nickel-recovery cost. This paper covers progress towards establishing such costs and, in particular, highlights the experimental work carried out in some of the nickel extraction techniques postulated.
$60.00